Vacuum Deposition
Vacuum deposition is a family of processes used to grow layers of material onto substrates under vacuum conditions. There may be multiple layers of different materials with thicknesses that can range from less than 1 nm to several microns. MBRAUN offers a number of products for thin film deposition applications. Our systems can either be glovebox integrated or offered as standalone units. Please choose from the following:
MB-ECOVAP
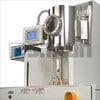
The MB-EcoVap tool is a high quality economic research solution when the available laboratory space is restricted. Even though compact in design all essential features for high-quality functional coatings are incorporated in its standard configuration, making it the perfect entry model for many research groups who have decided to take the first steps in exploring vacuum coating technology.
MB-PROVAP-3

The MB-ProVap-3 is a research and development tool for thin film deposition under vacuum conditions. The rectangular shaped chamber offers additional space for more sources and optional upgrades such as in-situ substrate heating and advanced masking solutions.
MB-PROVAP-5
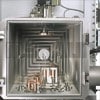
The MB-ProVap-5 is a versatile research and development tool for thin film deposition under vacuum conditions. The medium size chamber offers additional space for more sources and optional deposition tools such as in-situ, substrate heating and masking.
MB-PROVAP-7
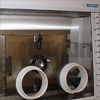
The MB-ProVap-7 is our large chamber research and development tool for thin film deposition under vacuum conditions. The large size chamber offers additional space for more sources and optional deposition tools such as in-situ, substrate heating and masking.
MB-OPTIVAP
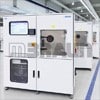
The MB-OptiVap series is the current high-end solution in MBRAUN’s deposition tool series. Designed for the requirements of specialized research up to pilot scale production, these tools find frequent use in industrial laboratories and state-of-the-art Universities throughout the world.
MB-SOURCES
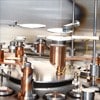
Thin film deposition systems by MBRAUN include a variety of ways of depositing layers of material onto substrates. Our systems can be custom configured to include different coating techniques to meet the customer’s exact specification.
SUBLIMATION
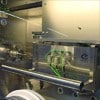
Modular Vacuum Sublimation Units provide the ability to purify up to 200 g per charge of volatile organic material (depending on density) for application in organic optoelectronic devices (e.g. OLEDs, organic photovoltaic’s) or nanotechnology.
Spin Coating
Usually deployed in R&D and pilot scale systems spin coating is a common technique used to apply uniform thin films to flat substrates. Usually an excess amount of a solution is dispensed onto the substrate, which is then rotated at high speeds in order to spread the fluid uniformly by centrifugal force. Rotation is continued while the fluid spins off the edges of the substrate, until the desired thickness of the film is achieved. The applied solvent is usually volatile and simultaneously evaporates. The achievable film thickness is a function of angular spinning speed, solid material content of the solution and the type of solvent.
Once spin-coating is complete, the plate is typically placed onto a hotplate (heated to somewhere between 80°C to 160°C) for several seconds or minutes to initially evaporate residual solvent and solidify the coating. Depending on the layer thickness and the solvent the substrate is then baked-out for several hours, or typically overnight, in a convection or vacuum oven, at a temperature high enough to sufficiently remove the remaining solvent.
Some materials are more difficult to coat than others. Most often poor quality, hazy, or “Mura defect” coatings are the result of moisture absorption due to environmental humidity. Strict control over the laboratory environment is the best way to improve coating quality, so the integration of spin coaters into gloveboxes or generally into inert gas equipment is preferable so that the sample does not have a chance to absorb moisture. For more demanding processes one should consider having the spin coater integrated into an inert, laminar flow enclosure to eliminate the disadvantageous effects of moisture and particles.
Major advantages of this technique are cost-efficiency, a limited set of process parameters to be controlled, low maintenance, ease of operation and adaptability to a variety of different processes. However spin coating reaches its limits when material usage and coating of large areas comes into consideration. Due to the process nature about 90% to 95 % of the feed material is spun off the substrate and is withdrawn from the process bowl as waste material. Especially in OLED applications where the active materials constitute a significant cost factor alternative coating solutions should be considered.
The MB-SC-200 is an easy-to-use spincoater for precise and uniform deposition of thin films and coatings. Its compact, vibration free and inertgas compatible design makes it a versatile and vital tool in every research facility.
As the industries only high end spin coater with the clear purpose to be integrated into a fully automatic inert enclosure the MB-SC-Advanced has set new standards in operating precision, programming flexibility, system control and productivity.
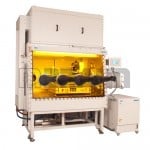
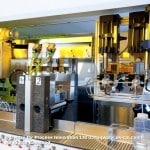
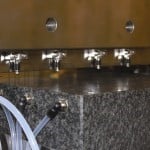
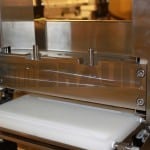
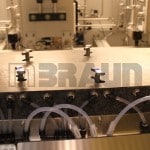
MBRAUN and its preferred partner network combined their specific expertise in inertgas technology and slot die coating in order to develop a tool that addresses the process requirements in emerging markets such like Organic Light Emitting Diodes (OLED), Organic Photovoltaic’s (OPV) and Thin Film Batteries. Available in a range of sizes to coat current and next generation substrates the MBRAUN Slot Die Coater (MB-SDC) allows for efficient, highly-uniform, spin-less coating of a wide variety of organic materials. Offering a robust platform and precisely machined components that create high material yields (>95%) along with minimal operating and maintenance costs. Many high-performance coaters like the MB SDC are applied in advanced research applications up to high volume manufacturing environments.
Smaller slot die coaters in this series are designed for substrates up to 200 x 200 mm whereas larger units are available for processing substrates up to gen 4.5 and beyond. Amongst a variety of optional features the patterning capability stands out from others. This technique provides the opportunity to deposit multiple, well defined coated areas on a single substrate. Almost any array of rectangular shapes can be coated on a single panel (within fluid property limitations) without the use of a mask. Instead the setup utilizes precisely machined shims incorporated into the die head which omit certain parts not allowing the fluid to pass through. It is supported by an enhanced PLC system for liquid flow control, die positioning and substrate alignment. Profile of the leading and trailing edges of each patch are adjustable to suit a variety of coating liquid characteristics.
- Able to coat organic or inorganic liquids on flexible or rigid substrates
- Available for R&D as well as gen2 through gen8 substrate processing
- Highly efficient process: technology ensures over 95% material use
- High throughput process
- Extremely accurate fluid dispense rates and volume control
- Coating thickness range from under 20 nm to >150 µm
- Minimal equipment footprint requirements
- Low Fill Volume option limits lot size of high cost polymers and other materials
- Multi-head configuration
- Pattern coating capability (stripes and rectangles
- Main control with graphical user interface (GUI)
- Optimized for OLED lighting applications
Please note: Specification may vary depending on configuration and model choice.
SUBSTRATE STAGE
- Granite base with active damping system; receiving pins; vacuum grooves for substrate fixation; stage flatness tolerance ± 2 μm
DIE HEAD STAGE
- Multi-head configuration available; motorized die head positioning system (positioning precision ± 1 μm) with integrated die-2-glass auto-alignment (coating gap accuracy ± 3 μm)
DIE HEAD
- Noncorrosive stainless steel; slit opening precision ± 1.5 μm
DISPENSE PUMP
- Programmable syringe pump; flow rate from 0.0001 μl/hr to 220 ml/min; flow rate accuracy ± 0.35%; reproducibility 0.05%
CONTROL UNIT
- Siemens S7-300 with touch panel (Mitsubishi control on request)
FILM PROPERTIES
- Material utilization > 95 %
- Wet film thickness from 1 μm up to 200 μm (depending on material)
- Dry film thickness from 1 μm up to 200 μm (depending on material)
- Viscosity range from 1 mPas up to 25,000 mPas
Ink Jet
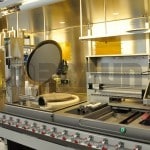

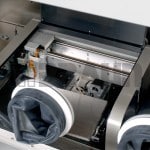
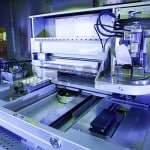
Inkjet printing is considered being one of the most versatile techniques in modern coating applications as it provides the opportunity to deposit all kinds of structures starting at the µm-level up to large area coatings. In principle the printing technology looks simple, but it is difficult to apply since it is composed of various technologies as well as the intrinsically complicated attributes listed below:
- Substrate treatment
- Inkjet printing head
- Product Manufacturing Process
- Device design
- Ink Jet printing system
- Jetting and printing process
- Post process
A crucial part in the inkjet technology is the ink itself, which dominates the quality, performance and reliability of the process. The uniformity and repeatability are the most important factors in sense of the inkjet printing system, jetting head as well as pre- and post-treatment processes.
Due to the complexity of this technique MBRAUN routinely works with industry leading and well-established companies that design, develop and manufacture piezoelectric inkjet print heads, assemblies, components and complete inkjet systems. Based on an in-depth understanding of the requirements of inkjet printing, MBRAUN has defined the integration standards and proven design rules that allow incorporating almost any kind of inkjet system into inert environments. From manually operated systems and semi-automatic solutions up to complete fully-automatic assembly lines MBRAUN has an inkjet printing integration solution for you.
Atomic Layer Deposition (ALD)
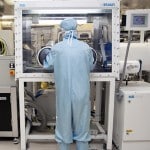
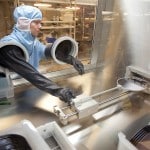
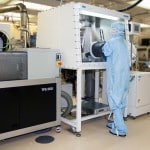
Atomic layer deposition (ALD) has emerged as an important technique for depositing thin films for a variety of applications. Semiconductor processing has been one of the main motivations for the recent development of ALD.
Based on an in-depth understanding of the requirements of ALD, MBRAUN has defined the integration standards and proven design rules that allow incorporating almost any kind of ALD system into clean environments. From manually operated systems and semi-automatic solutions up to complete fully-automatic assembly lines MBRAUN has an ALD integration solution for you.
MB-EBR
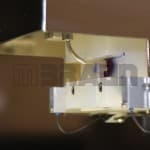
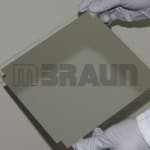

The MBRAUN Edge Bead Remover (MB-EBR) is specifically designed to solve the common problem of removing the boundaries of fully coated substrates. Cleaning the edges from organic layers is the prerequisite for an optimized subsequent encapsulation of the organic device. The removal process itself utilizes a high velocity solvent jet which is generated via the solvent jet nozzle. By directing the solvent jet towards the organic layer and moving the nozzle parallel to the substrate edge, a precise and accurate removal is achieved.
A custom exhaust system removes the organic debris immediately after it has been dissolved from the solvent jet, thus preventing any contamination of the remaining organic layer.
Special features include a self aligning and rotating substrate stage, a laser edge detection system, a fully PLC controlled process and the possibility to pre-define the width of the area to be removed. Different substrate sizes can be accommodated by replacing the substrate stage.
Edge bead removal for rectangular substrates
- Selective removal of organic layers
- Main control (PLC) with graphical user interface (GUI)
- Recipe programmable solvent jet nozzle (speed, position)
- Substrate top side solvent rinsing with solvent exhaust
- Automatic edge detection
SPECIFICATIONS
- Process type: Solvent jet with integrated vacuum exhaust
- Nozzle type: Solvent jet (no atomization)
- Removable border area: ≤ 15 mm (adjustable)
- Edge accuracy: ≤ ± 0.1 mm (depending on material)
- Substrate alignment: Non-contact pre-alignment (laser sensor)
Roll-2-Roll (R2R)
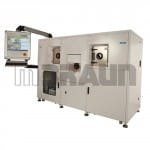
MBRAUN has developed a Roll-to-Roll (R2R) processing platform that is specifically dedicated for applications which require extremely thin coatings to be deposited onto a flexible matrix under high vacuum conditions. The core of the system is based on several rollers, called the web, around which the substrate is routed through the processing area.
Suitable substrate materials which are frequently used on this platform include metal foils such as aluminium, copper and molybdenum or plastic matrices like PET, PVC or POF. A comprehensive set of deposition sources ranging from sputtering, E-beam,
organic and thermal sources allow for coating an almost unlimited amount of materials.
Applications in solar, batteries, and OLED lighting currently convert existing processes into R2R as it helps cutting down overall manufacturing costs whilst driving up production rates and yields.
- High vacuum process conditions
- Roll-2-Roll process for a variety of flexible matrices
- In-situ substrate heating
- Co-deposition capabilities
- Comprehensive set of deposition sources
Specifications
- Roll length………………………..3500 mm
- Roll width…………………………100 mm
- Transport velocity………………0.1 mm/s up to 1.0 mm/s
- Vacuum level…………………….8*10-7 mbar
- Chamber leak rate……………..less than 10-9 mbar*l/s
- High vacuum pump……………oil diffusion pump with 5000 l/s